As Tata Steel UK embarks on a transformative £1.25 billion project to transition its steelmaking operations to low-carbon electric arc furnace (EAF) technology, it is poised to redefine sustainable steelmaking, creating value for industries like automotive while addressing the global climate challenge head-on. Peter Quinn, Tata Steel UK’s Director of Sustainability and Environment, reflects on the significance of this transition and its implications for the automotive industry.
Q: Can you tell us about your journey into the steel industry?
A: I didn’t plan a career in the steel industry. My background is in Environmental Science, which I studied at university because I was passionate about environmental issues. I was a member of Greenpeace at 14 and saw my future as campaigning to save the whales and stop the destruction of the rainforests!
An intriguing advert on a notice board at university led me to a graduate trainee opportunity in environmental research. I started working for British Steel (which became Corus, which itself became Tata Steel) as soon as I graduated from university in 1993. I’ve been with the same company, therefore, for 31 years.
I spent the first five years immersed in understanding pollutants, emissions control techniques, and environmental impacts in steelmaking processes. From there, my role has evolved – from environmental auditing to influencing climate and environmental policy.
Now, as Director, Sustainability & Environment, I lead a team of specialists responsible for sustainability and environmental policy, strategy and compliance across Tata Steel UK.
Q: What motivates you in your current role?
A: When I first started at Tata Steel over 30 years ago, I was deeply concerned with the environmental harm being caused by humans and wanted to "save the world." While I've had to reconcile my early idealism with the realities of working in heavy industry, my commitment to the environment has only grown stronger. The world needs steel to enable the transition to a low-carbon economy where people can enjoy a good standard of living – whether it's for renewable energy infrastructure, electric vehicles, or the built environment. But it's imperative that we produce that steel in a way that is sensitive to the needs of the environment. The importance of steelmaking to local communities and to national resilience is also abundantly clear. It’s those things that drive me.
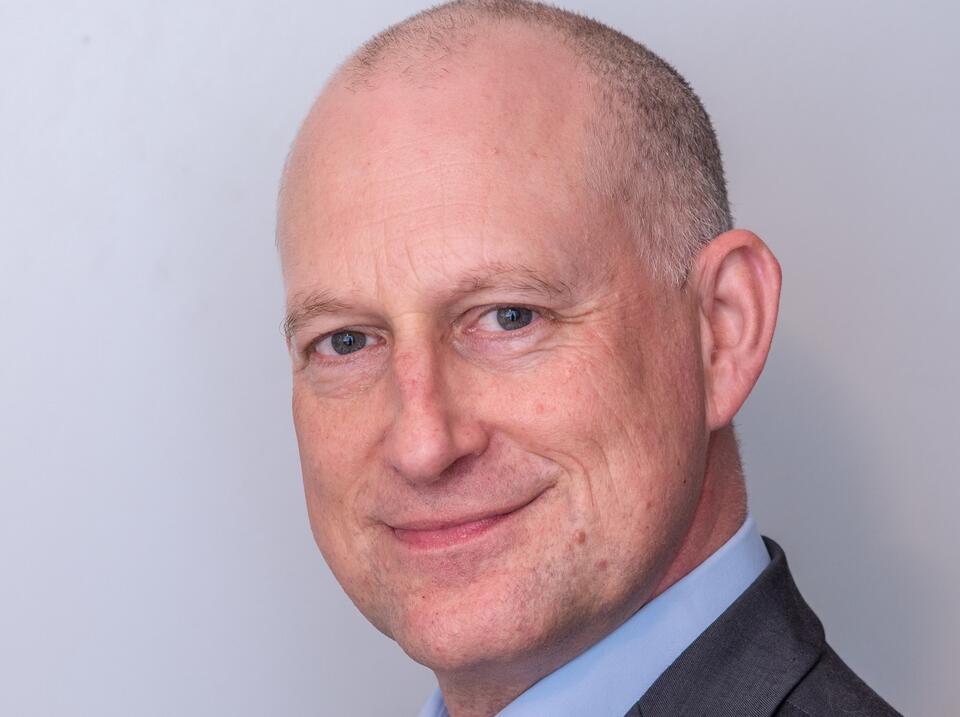
Q: What excites you most about Tata Steel's green steel transformation?
A: From what you now know about my background, you can probably understand why I find it so exciting that the steel company I’ve been with for thirty years is now on the brink of the biggest environmental transformation in its history. Tata Steel UK is poised to be one of the first strip steel producers in Europe to transition its operations to electric arc furnace (EAF) technology, which will allow us to reduce the CO2 emissions from Port Talbot by over 90%.
But it’s not just about reducing our own emissions. This transformation will also enable our customers across various industries to achieve their own sustainability goals. We’re not simply changing how we produce steel; we’re ensuring that steelmaking contributes to creating a sustainable future. For me, there’s no more meaningful way to bring my career full circle.
Q: What role does policy play in driving this transition?
A: Decarbonisation is a global priority, but policy frameworks and funding are crucial enablers. The UK government’s support for our EAF transformation reflects a broader trend: nations are investing in decarbonising critical domestic industries like steel because they recognise that without public co-investment, steel companies are unlikely to be able to make the transition to low-CO2 technologies. By supporting the transition, governments are locking in national resilience and self-sufficiency as well as the attainment of ambitious climate goals.
This support is vital. A £1.25 billion project of this scale wouldn’t be possible without substantial public funding. It’s an example of how private and public sectors can collaborate to drive meaningful change.
Q: How does the transition to EAF technology benefit the automotive industry specifically?
A: The automotive industry is increasingly focused on the embodied carbon in the materials used to manufacture vehicles. As we move towards electrification, tailpipe emissions decrease, and the carbon footprint of the production process thus becomes even more important. Automakers are looking to source steel with a lower carbon intensity to reduce the embodied carbon of their vehicles, and Tata Steel's EAF steel will be a game-changer for them.
This transition strengthens our partnerships with automakers, ensuring they have access to the materials they need to build the next generation of electric and sustainable vehicles, and giving them a competitive edge in the market.
Q: What are some of the myths or misconceptions about green steel production that you've encountered, particularly when engaging with automotive customers?
A: I personally don’t like the term ‘green steel’ as there is no universally accepted definition of what it means. What’s far more important is to have a detailed understanding of the embodied emissions in steel. This is why Tata Steel invests so much time and effort in life cycle assessment (LCA), which provides us with a means to understand the emissions and consumption of resources involved in the production of each tonne of steel. We have a steadfast commitment to providing our customers with detailed environmental information about our steel that enables them to compare our products with those of our competitors on a scientific and meaningful basis.
In terms of the technology, one common misconception is that EAF technology is some new ‘science fiction’ or untested technology. In reality, it's been around since the 19th century as a means of making many types of steel, so it’s fundamentally a well-proven and tested solution.
What makes our approach a little bit different is that historically, strip steel products have tended to be made from iron ore, using basic oxygen steelmaking convertors in conjunction with blast furnaces. However, we have watched closely as rapid advancements in EAF technology over recent decades have made it possible to produce high-quality strip steels via the scrap-based EAF route. It is this recent acceleration in technology that has enabled the exciting switch we are now about to make. With our new facility we will be able to produce high-quality flat steel products ranging from forming grades to advanced high-strength steels (AHSS) that meet the stringent requirements of the automotive sector. Rigorous testing is already underway, and we’re engaging with automakers to ensure we meet their needs throughout the transition to 2028 and beyond.
Learn more about how Tata Steel UK is transitioning to low-carbon steelmaking here.